Key Considerations for Automating Welding Processes
When embarking on the journey to automate your welding processes, several crucial factors come into play. These include understanding the specific welding application you're working with, evaluating the potential return on investment (ROI), and choosing the most appropriate robotic technology for your needs. This comprehensive guide explores the world of automated welding, robotic welding, and welding cobots, focusing on Formic Technologies' innovative solutions designed for manufacturing and co-packing facility automation.
Table of Contents
- Applications for Automated Welding
- Benefits of Robotic Welding
- Choosing the Right Welding Cobot
- Formic Technologies' Welding Solutions
- FAQs
Applications for Automated Welding in Various Industries
Automated welding technology is a game-changer that has penetrated diverse industries, each with unique challenges and prerequisites. The applications of automated welding are broad, featuring both industrial robots and collaborative robots (cobots) to optimize traditional methods and operational efficiency.
Manufacturing
In manufacturing, automated welding serves as a foundational technology, predominantly utilizing industrial robots for their high-speed capabilities. These robots excel in tasks like the fabrication of metal furniture, consumer electronics, and machinery, ensuring each weld is uniform and complies with stringent quality standards. By virtually eliminating human error, industrial robots contribute to waste reduction and more sustainable manufacturing practices.
Automotive
The automotive sector leverages both industrial robots and cobots in its automated welding processes. While industrial robots are calibrated for speed and precision, especially in the production of vehicle chassis, cobots are employed for tasks that require more intricate collaboration with human operators. Regardless of the type of robot used, the focus remains on the quality and safety of the welds to ensure all vehicles meet or exceed safety standards.
Get Your Free Getting Started Guide Here
Aerospace
In the aerospace sector, the high-stakes environment necessitates the use of both industrial robots and cobots for welding. Industrial robots are responsible for the heavy lifting and high-speed welding, especially when dealing with difficult-to-weld materials like composites and high-strength, heat-resistant alloys. Cobots are often used for more specialized tasks that require a high level of precision and might involve human-robot collaboration to ensure the structural integrity of components subjected to extreme stresses during flight.
Shipbuilding
In shipbuilding, automated welding is primarily done using industrial robots due to the large scale of the projects. These robots are programmed to execute complex, multi-layer welds that can withstand the corrosive maritime environment and the constant stresses of ocean travel. Here, the use of industrial robots ensures welds are both rapid and resilient, designed to resist corrosion and fatigue over the long term.
Infrastructure and Construction
The field of infrastructure and construction commonly uses both industrial robots and cobots for automated welding. Industrial robots are prized for their speed and the high-quality welds they can produce, which is crucial for meeting project timelines. Cobots, on the other hand, are used for tasks that require more finesse and may involve working in tandem with human operators, thereby maintaining the structural integrity of large, complicated constructions.
Benefits of Robotic Welding
The shift from manual welding to robotic welding comes with a myriad of advantages. One of the most significant benefits is increased efficiency. Robotic welders can operate continuously without breaks, thereby improving production speed and throughput. Another advantage is enhanced precision. Unlike manual welding, where human error can introduce inconsistencies, robotic welding ensures highly accurate and uniform welds. This level of precision significantly reduces the likelihood of defects and rework, leading to cost savings. Over time, the initial investment in robotic welding technology pays off through reduced labor costs, less waste, and increased output, making it a cost-effective solution for many businesses.
Benefits
- Eliminate headache of finding skilled workers
- Increase consistency and weld quality
- Reduce Cost of Goods
For the Following Businesses
- Metal Manufacturing
- Hardware Manufacturing
Examples
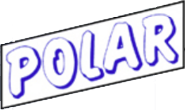
After seeing the success of their first Formic deployment (press machine tending), Polar Hardware continued to boost their production with Formic welding system.
“
We like formic because they don't just set up and walk away. They have skin in the game.
— Robert Albert
— President, Polar Hardware
Choosing the Right Welding Cobot
Selecting a welding cobot for your application is a critical decision that involves several factors. Firstly, you must understand the specific type of welding required for your application, such as MIG, TIG, or spot welding. The cobot you choose should be compatible with this welding type. Secondly, consider the payload capacity of the cobot. Make sure it can handle the weight and dimensions of the materials you'll be working with. Lastly, ease of programming is another essential criterion. Opt for a cobot with an intuitive user interface that allows for quick setup and seamless operation. These factors contribute to optimizing your automated welding processes effectively.
Fortunately for you, Formic’s team of experts can help you with every aspect of automating your welding process, ship the system to your facility, unload it, power it on, and help your team calibrate it all for no upfront cost or investment. You only pay by production hour (for a set number of hours depending on your needs), and Formic is also always available for maintenance and troubleshooting support!
Get Your Free Getting Started Guide Here
Frequently Asked Questions
What is the ROI of Implementing Robotic Welding?
Calculating the ROI of implementing robotic welding involves considering factors such as increased efficiency, reduced labor costs, and waste minimization. Generally, companies often see a return on their investment within one to two years due to these benefits. Formic also has an estimator on their site at Formic.co, and you save on upfront costs, maintenance costs, and training costs.
How Do I Choose Between Automated Welding and Manual Welding?
The choice between automated and manual welding boils down to your specific needs. Evaluate factors such as the production volume, precision requirements, and budget constraints. Automated welding is generally more suitable for high-volume, precision-dependent applications, while manual welding may be more appropriate for smaller, specialized tasks.
For more information on Formic Technologies' innovative robotic welding solutions, contact us today, or you can download our free guide on getting started with robotic automated welders below.
Download the Free Guide: How to Get Started with Robotic Automation
Automating with Formic, the only question manufacturers need to ask themselves is: what repetitive manual tasks can be automated in my facility right now?